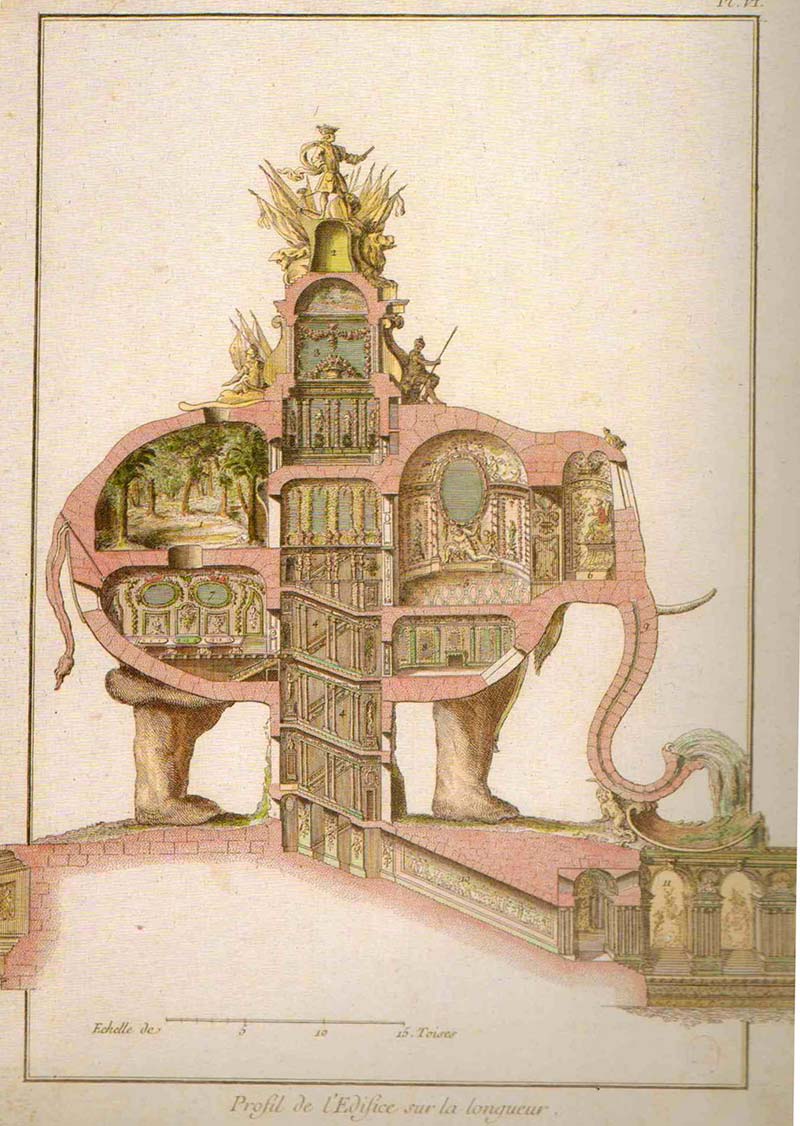
The Internet, mobile devices and cloud computing are drastically changing manufacturing. Software control systems embedded in smart devices and connected machines form a network of sensors and actuators that exchange information autonomously and can monitored and controlled online.
The potential impact of the Industrial Internet of Things (IIoT) and Industry 4.0 are undisputed. While industry pundits and technology vendors may dispute the exact size and growth rate of the IIoT, there is a general consensus that the space offers significant business value and will be transformative indeed.
Are the smart connected devices—or the “things”—that form the IIoT the same machines and devices we know and understand today, only connected? Or do we need to invent new paradigms to define system functionality and product architecture in order to realize the value of the IoT?
Design for IoT
At the most fundamental level, IIoT-based product development practices are transitioning from primarily mechanical engineering to systems engineering and the design of networked multidisciplinary systems.
We are approaching an era in which nearly everything and everyone is an IP node in an omnipresent communication cloud. Connectivity and security, and, for that matter, privacy, should be considered foundational requirements across all business functions, systems and product, and must be designed in, not bolted-on after the fact.
Multiple standards, including ISA95, Wi-Fi, and other near-field communication technologies, and IoT platforms such as GE Predix and PTC ThingWorx that support multiple interface standards natively, facilitate the design and incorporation of IoT controllers, sensors and actuators.
Furthermore, I expect the increased adoption of IIoT to accelerate the development of open-source implementations of standard protocol stacks using a variety of low-cost hardware and software such as the OpenWSN project and Libelium’s Waspmote.
Data Semantics is the Next Hurdle
While hardware connectivity and wireless communication can leverage IoT-related standards, the development and adoption of similar useful standards for data semantics lag behind. Proprietary data formats and definitions of sensor information and actuator controls require significant level of customization, data manipulation, and development of bespoke analytic models and control software, increasing the effort and time to value of IIoT implementations.
Design for the Business of IIoT
Designing an IIoT device should not only consider the connectivity and data communication aspects we discussed earlier, but, as importantly, it should guide and influence the design of IOT devices. Design for IoT must incorporate the business model into the design. It should consider the role of the device in a customer-centric business solution and how it might influence operational strategy and decision making throughout its lifecycle.
The following examples illustrate design for IoT thinking in the design of equipment maintenance service:
- Onboard and remote diagnostics, and remote software update tools are designed to meet aggressive service level agreement (SLA) goals for asset uptime and service responsiveness. This is an opportunity for the service organization to improve the profitability of extended service contracts.
- Remote diagnostics are aligned with hardware modularity, field replaceable unit (FRU) and spare part inventory management policies. There’s little point in identifying a failure remotely unless it can be mapped to an available spare part.
- Remote service offers numerous opportunities for workforce management optimization. In particular, it helps maximize the utilization of technical support experts and allows more flexible allocation of available field service personnel. Design of IoT-based service can help alleviate some of current and anticipated challenges in workforce availability, skill distribution and training.
Retrofitting Old Equipment
As I often point out to those that have an overly rosy view about the potential size of the IIoT market, market growth is gated by the ability to incorporate existing manufacturing assets into the IIoT network. The average age of industrial equipment in the U.S. is approximately 12 years, the highest since 1938. Many factory floor manufacturing machines and industrial equipment are much older and lack the basic functionality to be connected and monitored remotely, but still have a very long service life ahead of them.
All too often the response is to add sensors, data acquisition hardware and communication to those aging factory machinery, assembly lines and manufacturing assets. In most cases this type of retrofitting is highly impractical.
First, one cannot simply super-glue a sensor onto a piece of equipment and connected it the Internet. The correct placement of a sensor requires hardware and software redesign, and expensive onsite retrofitting work, one piece of equipment at a time.
More importantly, retrofitting a piece of equipment in service means taking it out of production for a significant amount of time, which, for most companies, isn’t an option.
Design for IoT or Design by IoT?
Most engineering organizations lose sight of their products once they are sold or installed in the field. In some manufacturing companies this can happens at an earlier stage, when a product just enters volume production.
Product organizations cannot have a true and complete view of a product and how customers are using it unless they can continue to observe it while it is in use.
The IIoT helps address much of this myopia.
Engineering organizations use digital models during early product design phases to test the design, evaluate alternatives and communicate with suppliers. More sophisticated organization extend this “digital twin” to evaluate human-machine interaction and product ergonomics. Yet others use it to design and accelerate the ramp up of the manufacturing process. But, again, these activities usually wind down when a stable design enters volume manufacturing.
With IIoT-enabled products, the process doesn’t end. Products and users continue to provide information throughout the lifecycle, adding rich multidisciplinary information that extend beyond design information and includes multifaceted data from manufacturing, supply chain, service and maintenance. The digital twin becomes then a model that “experiences” the physical product, in real time if necessary, throughout its lifecycle.
Using the digital twin, various product groups have an ongoing view of product operation and quality, service operations, customer interactions, and how well the product meets market needs and customer expectations. Essentially, instead of the traditional linear model in which early design concepts and prototypes are tested against relatively static and often stale product requirements and focus groups, the IoT-driven digital twin creates a live perpetual focus group for each key product lifecycle function that facilitates improvement of both current and future products.
Image: Elephant Monument for Champs-Élysées (Jean-Jacques Lequeu, 1758)