A Tribute to Pareto, Juran, and the 80/20 Rule
The “80/20 rule” has become ubiquitous in everyday business language. This rule, or rather an axiom, states that roughly 80% of the effects come from 20% of the causes. For instance, we might say that 20% of the employees do 80% of the work, or 20% of the quality problems account for 80% of the scrap. Many refer to the 80/20 rule as “Pareto’s Law.”
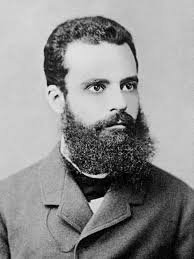
Vilfredo Pareto (1848-1923)
Vilfredo Pareto (1848–1923) was an Italian social-economist who argued that people are physically, intellectually and morally unequal. Pareto maintained that in society as a whole, and in any of its classes and subgroups, some people are more capable than others. The most gifted in any grouping form the “elite” of that group.
Pareto’s original use of the term “elite” did not mean specific social connotation; it simply denotes “a class of the people who have the highest indices in their branch of activity.” He divides the elite class into two classes: “a governing elite, comprising individuals who directly or indirectly play some considerable part in government, and a non-governing elite, comprising the rest.” According to Pareto, society has a tendency to maintain equilibrium, and people are entering and leaving the elite to maintain the natural balance.
Pareto is best known for his “Pareto’s Principle” of income distribution. He found that about 20% of the wealthiest people in Italy owned 80% of the land, which led him to conclude that in all countries and times, the distribution of wealth follows a similar pattern. Indeed, if we total the GDP of the world’s richest countries, we find that 20% of the world’s wealthiest people control nearly 90% of the wealth.
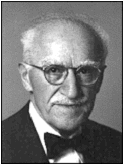
Joseph Juran (1904–2008)
Quality management pioneer Joseph Juran (1904–2008) recognized a universal principle he called the “vital few and trivial many”: 20% of the causes are responsible for 80% of the results. In his 1950 article “Pareto, Lorenz, Cournot, Bernoulli, Juran and Others“, which appeared in the book Critical Evaluations in Business and Management, Juran incorrectly applied Pareto’s socio-economic observations to this broader observation and named it Pareto’s Principle.
In 1974, Juran published an article titled “The Non-Pareto Principle; Mea Culpa“, in which he wrote:
The “Pareto principle” has by this time become deeply rooted in our industrial literature. It is a shorthand name for the phenomenon that in any population which contributes to a common effect, a relative few of the contributors account for the bulk of the effect.
Years ago I gave the name “Pareto” to this principle of the “vital few and trivial many.” On subsequent challenge, I was forced to confess that I had mistakenly applied the wrong name to the principle. This confession changed nothing – the name “Pareto principle” has continued in force, and seems destined to become a permanent label for the phenomenon.
The matter has not stopped with my own error. On various occasions, contemporary authors, when referring to the Pareto principle, have fabricated some embellishments and otherwise attributed to Vilfredo Pareto additional things which he did not do. My motive in offering the present paper is in part to minimize this tendency to embroider the work of a distinguished Italian economist. In addition, I have for some time felt an urge to narrate just how it came about that some early experiences in seemingly unrelated fields (quality control, cryptanalysis, industrial engineering, government administration, management research) nevertheless converged to misname the Pareto principle.
As Juran wrote, the incorrect name of the principle does not change the validity of the notion the vital few and trivial many. Focus your attention on the few vital elements in your business that promise the most important result, and avoid the common trap of trying to improve issues that may be very visible but improving them will have only an inconsequential effect. This might be a good lesson for some Six Sigma zealots: Not every highly variability process is worth attenuating.