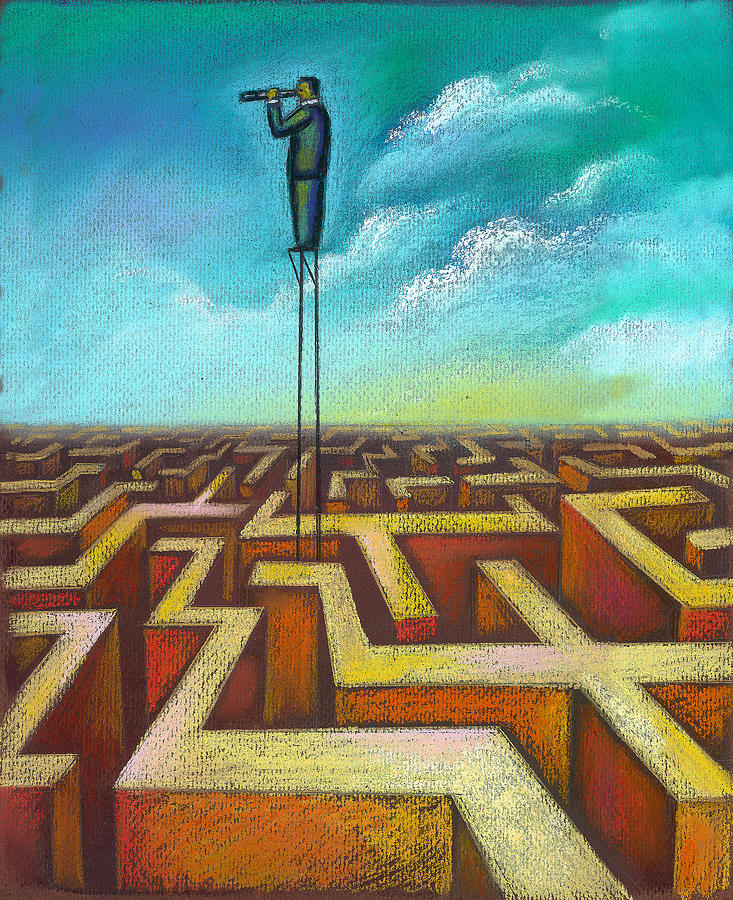
The Race to Reinvent the Process for Developing Connected and Autonomous Vehicles
Forward-looking automakers are recognizing how the convergence of technology, business, and societal trends is transforming the automotive industry, posing an unprecedented level of new opportunities as well as unfamiliar threats. These manufacturers have already begun to refine their structure and processes to embrace the changes, face the threats, and build organizations that can deliver on the ever-changing possibilities for new mobility solutions for customers.
Industry in Flux
Just over 100 years ago, Henry Ford disrupted the auto industry of the time with the introduction of the mass-production moving assembly line. To say that the auto industry is again in flux is almost cliché. Most everyone is aware of the massive changes the industry is undergoing, although the cumulative long-term effect of rapid technology innovation, disruptive business models, and evolving supply chain ecosystems is probably not fully comprehended yet.
Vehicle technology is undergoing rapid change, requiring a new approach to design engineering and the management of the supply chain. The opaque and inefficient systems and processes used to design and manufacture cars today will not carry the industry forward in its next century. A new approach is needed, an approach that for some might be as radical as the introduction of moving assembly lines a hundred years ago, along with the boldness to take the first steps down this road.
Computers on Wheels?
We see more change in the next five years than there’s been in the last 50 —Mary Barra, CEO, General Motors (and numerous others…)
The expression “modern cars are just a computer on wheels” may be a gross generalization and oversimplification that ignores the large number of mechanical parts and subsystems responsible for everything from suspension and steering to passive safety, but the general sentiment is, of course, correct. Modern cars are loaded with advanced electronics and complex software systems that control active safety features, steering and braking systems, and the car’s infotainment and communication equipment.
But the most profound change in the auto industry is being driven by the emerging notion of connected and autonomous cars. Industry visionaries and practitioners alike have a bold vision of a future in which cars, occupants, and cloud-based systems communicate and exchange information in the omnipresent Internet of Things (IoT) cloud, or, in today’s parlance, they are yet additional “things” in the Internet of Things.
Behind this, an increasing number of functional and user experience features are being implemented in software. In fact, by some measures, software is now the dominant component in vehicles and its importance continues to expand. But the magnitude and complexity of embedded control software is stressing the organic ability of OEMs and suppliers who are struggling to update engineering systems and processes, reskill, and ramp up software development.
New Automakers Rising
Tesla is well-recognized as the automaker that managed to successfully challenge the hegemony of traditional automakers and is making rapid progress towards bringing autonomous vehicles to market. Although it is still fighting volume manufacturing issues and does not have the global footprint of established OEMs, Tesla has the deep pockets and tenacity to see these through. Tesla succeeded where others before it had failed and showed that traditional OEMs are not invincible.
In emerging markets, especially in China, the number of OEMs is growing rapidly. Free of the legacy of the past 100 years, Chinese OEMs are laying the foundation for expansion by acquiring global brands and targeting autonomous and electric vehicles. There are over 100 passenger car brands available in China from local automakers and joint ventures with global OEMs and suppliers. Although these manufacturers have mostly regional ambitions, they represent a real threat to global OEMs coveting the lucrative China market, which is growing by an average of 7% year over year and, in 2020, is expected to reach annual sales of 25 million vehicles.
Suppliers are no Longer Just Suppliers
We are evolving into a provider of services for road users. To come up with new concepts for mobility, we are also revising our conception of Bosch. –Rolf Bulander, Chairman of Bosch Mobility Solutions
Rapidly emerging vehicular technologies, from electric propulsion to active safety and autonomous driving control systems, are shaping the future of the automotive industry. Both traditional and aspiring suppliers are taking a center role in the automotive value chain, because they are very much in control of the hottest technologies. Like OEMs, forward-looking suppliers also understand the tectonic shifts in the automotive industry and are restructuring to seize other opportunities in the evolving mobility space.
For example, the automotive industry is emerging as the next largest volume market for semiconductors, driving semiconductor companies to invest heavily in sensors, especially in video and solid-state LIDAR, and in high-bandwidth single-chip sensor fusion components.
The volume of activity is attracting companies such as NVIDIA, Qualcomm, and Intel, which, until recently, preferred to stay away from direct involvement in the automotive supply chain and were happy to sell components to lower-tier suppliers.
Software Development as a Strategic Capability
It’s not hard for me to predict that we’ll have more software engineers than mechanical engineers at the company within the next five years. —Klaus Hoehn, Vice President of Advanced Technology and Engineering, John Deere
Developing simple control software in the earlier generations of automotive systems wasn’t a very onerous task. OEMs and suppliers managed through the process using rudimentary software engineering environments built around open-source tools, spreadsheets, and email communication.
But as software has grown in complexity, from controlling mechanical subsystems to being the key differentiator for the customer experience, the number of software related recalls is increasing rapidly, showing that the industry is struggling in this critical area. J.D. Power’s SafetyIQ reported that the number of technical service bulletins (TSBs) pertaining to software issues increased from an average of 58 per year between 2006 and 2010 to an average of 160 per year from 2011 through 2015.
The Systems of Systems Conundrum
Cars were always an assemblage of mechanical, electrical, and hydraulic and pneumatic subsystems. These systems were unsophisticated compared to todays advanced technology and their integration was sufficiently straightforward that they could be designed, prototyped, and validated using traditional mechanical engineering methods.
Automotive engineering began experiencing a major shift in the late 1980s, as advanced vehicle electronics and embedded control software were introduced into cars to handle increasingly stringent emission regulations. Nowadays, embedded control and user interface software govern practically all aspects of both vehicle operation and driver experience.
Vehicle control systems are no longer a small number of loosely-coupled components with simple interfaces. They are large-scale concurrent and distributed systems involving multiple engineering disciplines, with complex system interactions that are difficult to simulate and test thoroughly and often expose design and interoperability weaknesses.
Furthermore, one of the biggest motivations to utilize software-based functionality is the ability to deliver easily configurable customer options. However, combined with a large portfolio of trim options, this strategy results in a practically infinite number of vehicle variants and customer options that must be tested and validated individually.
Today’s Model Won’t Scale
These rapid changes are stressing engineering methods, processes, and tools that, by and large, have not kept up with the new disciplines and the growing complexity of systems development.
Design engineering and test environments based on decades-old systems and tools, supplemented by ad hoc use of informal tools such as spreadsheets and email communication will not meet the challenges involved in developing complex vehicle systems.
While small and agile engineering teams may be able to overcome gaps in formal tools and methods, and, in fact, be very effective in using unstructured tools and manual processes, this practice does not scale. An informal nimble team can quickly become sluggish and inefficient in dealing with external supply chain partners and responding to new business opportunities.
The New Era of PLM
Product Lifecycle Management (PLM) software was meant to be the major repository to connect users to critical information and support collaboration across-disciplines within the extended enterprise, from design to manufacturing and in-service. But the fragmented architecture and inflexibility of legacy PLM systems, where multiple systems must be deployed to support applications, makes it hard to scale across the enterprise – hence the widespread use of spreadsheets and accompanying lengthy email threads and contentious meetings to attempt to plug the gaps.
Given the nature of technological change facing automotive companies, there is no longer room for data silos and fragmented processes in the product lifecycle. Companies must adopt a systems engineering orientation with the management of mechanical, electrical, and software disciplines.
PLM is emerging, again, as the product innovation platform to model and manage all logical connections between requirements, design information, simulation results, test data, and other product lifecycle artifacts. The product innovation platform provides through-life management of product configurations, designs and processes.
A common PLM platform enables uniform access to authoring tools and exchanges information with enterprise systems, automates manual processes and provides migration and translation from legacy systems. With integrations for enterprise software systems such as PDM, ALM, CAD, and ERP, this next generation platform connects all users into a single set of information and processes.
While companies should have low tolerance to data silos and must work to establish processes that leverage a common platform, the reality is that eradicating fragmentation completely is probably unattainable. In part, because of the board set of methods and tools, and in part due to new value chain participants in product lifecycle management process and practices. Some, such as the Internet of things (IoT) are truly newcomers, whereas others, for example service lifecycle management (SLM), are not necessarily new, but are finally claiming their rightful role in product lifecycle decisions.
Therefore, PLM, as an innovation platform, must remain open and able to integrate these and other objects, data types and processes in a way that creates rich multidisciplinary context and enables frontloading key decisions requires extending the semantic model of PLM software.
Change is Inevitable
Yes, there’s a lot at stake. Yes, there is a lot of uncertainty. But this is not a time for the conservative or the cautious. —Carlos Ghosn, Chairman and CEO, Renault-Nissan Alliance
Nothing in the traditional automotive business, which has remained relatively unchanged for many decades, is safe anymore. Everything is fair game, and OEMs are no longer the masters of their destiny. Industry relied on internal innovation, manufacturing and supply chain complexity as barriers against outsiders. This will not be sufficient going forward.
Organizations are recognizing that they must undertake a digital transformation of their product development processes. But we must recognize that these changes, especially for large organizations with a deeply engrained culture that for many years seemed to be working well, are difficult.
But these changes are unavoidable. Automotive OEMs and their suppliers that embark on this journey now will be in a much stronger position to realize the enormous growth opportunities of the digital age creating opportunities for innovative products, services, and business models.
Image: Focal Point (Leon Zernitsky)
This article was also published here https://www.aras.com/resources/white-papers/youre-not-going-to-get-there-from-here