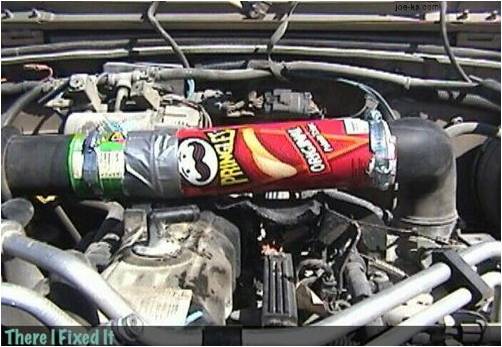
The Cost of Poor Service
Maintaining, servicing and repairing complex vehicle systems is a growing challenge. Much has been written on service metrics and operational performance, but it’s worthwhile to pause to highlight few figures to understand the impact that service (poor service, that is) has on the bottom line. The following data are from multiple research studies I conducted in automotive and aerospace repair operations:
- Typically, auto repair shops are able to fix about 80% of the cars during the first customer visit. While about third of the dealerships are able to deliver better than 90% first time fix (FTF) rate, nearly 20% of all dealership manage only abysmal FTF of less than 70%.
- When repairs activities are audited by the OEM for warranty reimbursement and quality assessment, 37% of replaced parts do not exhibit any problem and are identified as “no fault found” (NFF).
- In commercial aviation, approximately 40% of mechanical parts and 60% of avionics parts are classified as NFF.
Poor service performance levies significant financial and logistics burden on OEMs and has critical influence on brand image and customer loyalty. Still, OEMs don’t always feel they realize sufficient return on the efforts to develop advanced diagnostic tools, training and service manuals, and with the continued pressures for increased profitability, justifying further investment in service tools can be difficult.
No Fault Found
Understanding the issues that produce NFF parts sheds light on the root causes of suboptimal service:
- In the course of a service call, a technician replaces multiple parts; however only one of these parts is the actual root cause of the failure. Excessive part swapping as a fault isolation technique often indicates ineffective diagnostic procedures, poor service information and deficient training.
- On the other hand, there are instances where part swapping is permissible or even required. For instance, when equipment uptime is paramount and the higher cost of the repair (and of NFF parts) is tolerable.
- Marginal product design leads to “tolerance stacking” in which parts interaction will generate a failure in some fielded system but not in others or on the test bench.
- Imprecise diagnosis or incomplete repair appears to fix the problem temporarily. For example, the replacement of an electronic part temporarily corrects a problem caused by a faulty connector. The removed part will be tested to be NFF, and the equipment will eventually fail again.
Serviceability and Maintainability
These examples highlight the need for improved diagnosability and maintainability characteristics of complex equipment:
- Accurate diagnostic tests to reduce the number of replaces parts and minimize part swapping as a diagnostic technique.
- Adequate repair verification methods to ensure a precise and complete repair and to improve equipment uptime and FTF.
Difficult Decisions
While the benefits of design changes and enhanced on-board and off-board diagnostic aids are sufficiently obvious, it is equally clear that they require additional design, simulation and testing efforts that are likely to increase the time to market and the cost of the end product.
Brand owners and product companies face a predicament: How to gauge the incremental cost of the upfront investment against the long term benefits?
SAE J817
Organizations often lack the tools and metrics to assess the maintainability characteristics of a piece of equipment. They need an objective yardstick to perform comparative ‘what-if’ analyses of alternative designs and weigh them against upfront cost and potential improvement in key service indicators such as FTF and NFF.
SAE J817 standard is intended to provide a uniform methodology to assess the maintainability features of a piece of equipment—primarily off-highway and automotive—and generate a Maintainability Index: an objective and consistent point system ranking of equipment maintainability.
Work on J817 is ongoing. In its current form, the standard doesn’t offer a comparable methodology to assess diagnosability using metrics that include:
- The number of potential root causes per symptom, and the corresponding number of field replacement units (referred to as the ambiguity set.)
- The efficacy and efficiency of onboard and off-board diagnostic tool in iteratively reducing the size of the ambiguity set.
- The effectiveness of verification methods.
Service Lifecycle Management
Industry will benefit from improved methodologies and standardized approaches to evaluating and ranking diagnosability and maintainability. Unfortunately, many maintainability related standards and methods in use today date back to the 50s and 60s and have not been updated to handle the exponential increase in equipment complexity which is largely driven by electronics and embedded software.
The industry is undergoing renewed emphasis on the business benefits of service lifecycle management (SLM) and the migration towards the design of smart connected devices to form Internet of Things (IoT) networks. Further enhancements in equipment design and methods to improve diagnosability and maintainability will help realizing those benefits.
[Image source: There, I fixed it]