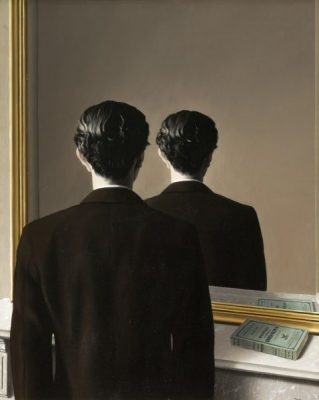
Yes, I know, one should not predict the future from history. But I recently came across a Forbes article from five years ago and thought that as we take stock of the last decade and starting a new one, it is worth visiting.
In 7 Lessons from the Internet of Things Frontier, an Oracle marketer claims that 90% of the companies looking to launch an Internet of Things initiative want their system delivered via cloud software and infrastructure. The author offers seven insights, presumably based on actual customer implementations, which are summarized below along with my comment.
- Select your cloud software and infrastructure. Selecting a cloud provider is a key decision in IoT implementation. Remember, the article was published in 2015, when Oracle was aggressively pushing cloud-based SaaS and PaaS products.
- The conversation about IoT always starts with the device. Early adopters begin by thinking about device connectivity and cybersecurity but neglect to define the expected business outcome. This was true then and, unfortunately, still is.
- Companies are thinking cloud-first, but many want the option to bring operations on premises. The article is playing it safe. While promoting a cloud-first strategy, it reminds Oracle users who want to stay on-prem “there as a check-the-box, to mitigate the risk.”
- When Internet of Things initiatives fail, it’s usually because they can’t scale. The author makes an argument for the reliability of Oracle’s cloud platform and infrastructure, and the commitment of the company to robust performance.
- Beware the left hand (marketing) not knowing what the right hand (operations) is doing with IoT. Here, the author cites an example of a grocery chain whose management was not aware of two IoT initiatives going on in parallel with different business goals and no collaboration.
- There is “a ton of money to be made in mitigating risk” using IoT systems. This enthusiastic claim is referring to the frequently used IoT use case of preventing unplanned downtime of critical assets. To be exact, the “ton of money” isn’t money made but rather money saved in reducing the cost of unscheduled maintenance.
- Companies realize they can’t wait for IoT data standards to emerge. As is often the case in emerging technologies, lack of standards (or, in the case of IOT, perhaps too many of them) can lead to lengthy and costly implementation. Ironically, the Oracle partner cited in this article uses its own protocol for IoT communication and integration. What can I say?
It’s March 2020
So, where are we five years later?
Cloud
To the disappointment of many, the observations made by the Forbes article five years ago are as relevant today as they were then. One notable exception though is the adoption of the cloud. While adoption of cloud technology in manufacturing has been lagging behind other sectors, it is gaining momentum. Legacy IT and concerns about data security and compliance, coupled with shortage of skilled personnel continue to be a challenge, but most organizations across all sectors are tracking the increasing adoption of cloud-first strategies.
Many manufacturing organizations today are as busy as they were five years ago with infrastructure connectivity and cybersecurity, often at the cost of a weak business case. Consequently, these initiatives manage to demonstrate the value of IoT in a lab environment, but die shortly thereafter.
Predictive Maintenance
The most disappointing aspect of our visit to the IoT world of five years ago, is that the use of IoT to monitor equipment and provide early warning to reduce or even prevent unplanned downtime is still the lone use case vendors can talk about in detail. And yet, large scale “industrial grade” predictive maintenance implementations are scarce.
More Technology…
The irony is that IoT vendors not only continue to focus on IoT technology instead of business outcomes, they keep adding to it. Over the past few years augmented and virtual reality were promoted aggressively as the technology that will finally accelerate the adoption of IoT in manufacturing and service (which hasn’t happened yet). Incorporating AR and VR indiscriminately in the IoT technology stack (which I don’t think is accurate) only adds complexity and cost.
The current excitement over artificial intelligence and machine learning is yet another example. While using AI to harvest value from the wealth of data provided by IoT can be potentially beneficial, it isn’t critical and is certainly not the reason why IoT adoption is behind vendors’ expectations.
How Many Devices will be Connected to the Internet by 2030?
And in the interim, industry analysts are as busy today as they were five years ago at the old game of guessing (unsuccessfully) the number of connected devices in the future. While some organizations will certainly benefit from the increase in the number of connected devices and the data traffic they generate, these statistics are of no significance to most manufacturing companies.
Manufacturing Industry Cadence
While perhaps disappointing, it should not come as a surprise that the manufacturing industry appears to be slow in actual implementation of industrial IoT and Industry 4.0. What many proponents of IoT underestimate is that despite the attractive promise of the industrial IoT, the manufacturing industry is operating at a certain cadence that cannot be easily accelerated. Beyond the sheer complexity of the organizational transformation dictated by IoT, the simple fact is that most manufacturing plants are old, and modernizing brownfield factories can be a difficult endeavor.