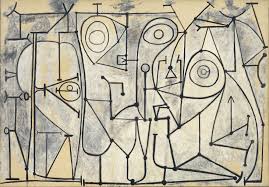
Engineering change orders – ECOs, ECNs, ECRs, whatever you call them—are a key activity during design and volume ramp up stages and continues well into the product’s useful life. In many organizations, ECOs are the heartbeat of the product development process, indicating how well the product organization defines and implements requirements, follows design guidelines, understands and implements manufacturability best practices, and meets stringent quality standards. I have worked with manufacturing companies that use the ongoing number of ECOs as a measure design maturity and an indicator when the design is ready to start transitioning to manufacturing. I disagree with this methodology, but that’s a subject for another blog post.
Fundamentally, ECOs reflect errors in requirements definition, design or manufacturing. They represent waste in the product development process. ECOs are disruptive and resource intensive, and mature organizations should make an effort to minimize the frequency and impact of ECOs.
Admittedly, with the time and resource pressures most manufacturing organizations face, some ECOs are perhaps inescapable, at least not in any business-practical way. On the other hand, research shows that many ECOs are caused by poor adherence to established best practices, overzealous engineering, and nonconformance with downstream guidelines and resources; all issues that should be quite straightforward to circumvent.
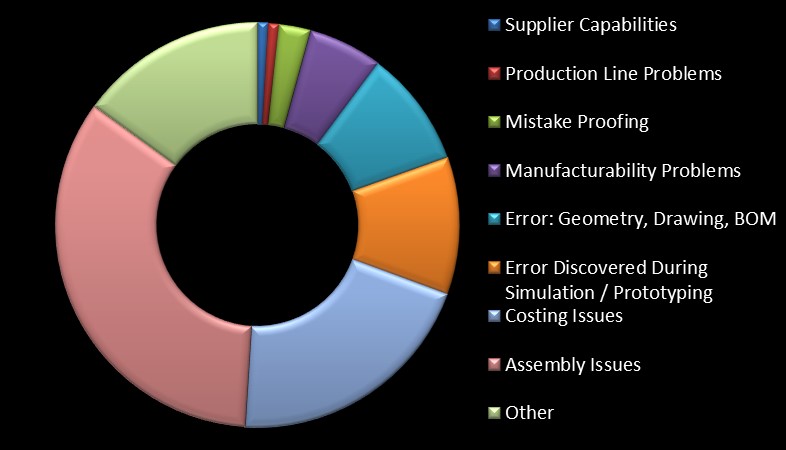
I recently reviewed an analysis of more than 2,000 ECOs at an industrial equipment manufacturing company created over the course of three months. The chart shows the breakdown of ECOs are preventable using reasonable process improvement tools and those that are inherent to the process and therefore not easily eradicated. The data suggests that nearly 70% of the ECOs fall under various preventable categories.
Following that analysis, this manufacturing company implemented aggressive design for manufacturing (DFS) measures. A conservative estimate suggests that these and related improvements will save approximately $15M annually. Process improvement and saving opportunities in your organization are going to be different, and you’d need to perform a similar analysis to estimate the potential savings that an improved process will yield, but I believe that 30-50% reduction in the number of ECOs is an achievable target.
Image: The Kitchen (Pablo Picaso, 1948)